In 2015, Tim Ellis and Jordan Noone founded Relativity Space around an ambitious goal: to be the first company to put a 3D printed rocket into orbit. While additive manufacturing was already becoming an increasingly important tool in the aerospace industry, the duo believed it could be pushed further than anyone had yet realized.
Rather than assembling a rocket out of smaller printed parts, they imagined the entire rocket being produced on a huge printer. Once the methodology was perfected, they believed rockets could be printed faster and cheaper than they could be traditionally assembled. What’s more, in the far future, Relativity might even be able to produce rockets off-world in fully automated factories. It was a bold idea, to be sure. But then, landing rockets on a barge in the middle of the ocean once seemed pretty far fetched as well.
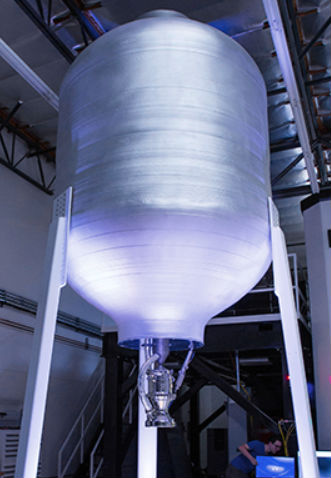
Of course, printing something the size of an orbital rocket requires an exceptionally large 3D printer, so Relativity Space had to built one. It wasn’t long before the company had gotten to the point where they had successfully tested their printed rocket engine, and were scaling up their processes to print the vehicle’s propellant tanks. In 2018 Bryce Salmi, then an avionics hardware engineer at Relatively Space, gave a talk at Hackaday Supercon detailing the rapid progress the company had made so far.
Just a few years later, in March of 2023, the Relativity’s first completed rocket sat fueled and ready to fly on the launch pad. The Terran 1 rocket wasn’t the entirely printed vehicle that Ellis and Noone had imagined, but with approximately 85% of the booster’s mass being made up of printed parts, it was as close as anyone had ever gotten before.
The launch of Terran 1 was a huge milestone for the company, and even though a problem in the second stage engine prevented the rocket from reaching orbit, the flight proved to critics that a 3D printed rocket could fly and that their manufacturing techniques were sound. Almost immediately, Relativity Space announced they would begin work on a larger and more powerful successor to the Terran 1 which would be more competitive to SpaceX’s Falcon 9.
Now, after an administrative shakeup that saw Tim Ellis replaced as CEO, the company has released a nearly 45 minute long video detailing their plans for the next Terran rocket — and explaining why they won’t be 3D printing it.
Continue reading “Relativity Space Changes Course On Path To Orbit”