[Angus] of Maker’s Muse has a video with a roundup of different 3D-printable hinge designs, and he points out that a great thing about 3D printing objects is that adding printable features to them is essentially free.
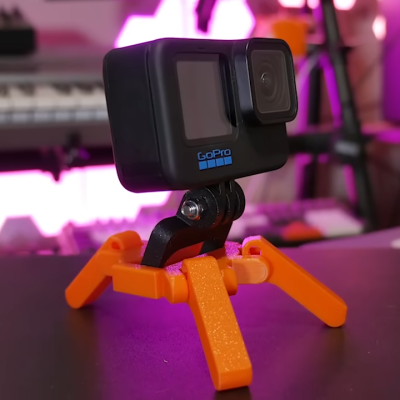
A great example of this is his experimental print-in-place butt hinge with indexing feature, which is a hinge that can lock without adding any additional parts. The whole video is worth a watch, but he shows off the experimental design at the 7:47 mark. The hinge can swing normally but when positioned just right, the squared-off pin within slots into a tapered track, locking the part in place.
Inspired by a handheld shopping basket with a lockable handle, [Angus] worked out a design of his own and demonstrates it with a small GoPro tripod whose legs can fold and lock in place. He admits it’s a demonstration of the concept more than a genuinely useful tripod, but it does show what’s possible with some careful design. Being entirely 3D printed in a single piece and requiring no additional hardware is awfully nice.
3D printing is very well-suited to this sort of thing, and it’s worth playing to a printer’s strengths to do for pennies what one would otherwise need dollars to accomplish.
Want some tips on designing things in a way that take full advantage of what a 3D printer can achieve? Check out printing enclosures at an angle with minimal supports, leveraging the living hinge to print complex shapes flat (and fold them up for assembly), or even print a one-piece hinge that can actually withstand a serious load. All of those are full of tips, so keep them in mind the next time you design a part.