If your shop is anything like mine, you’ve got a large selection of colorful cans claiming to contain the best and absolutely only lubricant you’ll ever need. I’ve been sucked in by the marketing more times than I care to admit, hoping that the next product will really set itself apart from the others and magically unstick all the stuck stuff in my mechanical life. It never happens, though, and in the end I generally find myself reaching for the familiar blue and yellow can of WD-40 for just about every job.
Author: Dan Maloney3304 Articles
AV Remote Control Teams Arduino With – Visual Basic?
A large installed base of powered speakers from a defunct manufacturer and a dwindling supply of working remote controls. Sounds like nightmare fuel for an AV professional – unless you take matters into your own hands and replace the IR remotes with an Arduino and custom software.
From the sound of it, [Steve]’s crew was working on AV gear for a corporate conference room – powered speakers and an LCD projector. It was the speakers that were giving them trouble, or rather the easily broken or lost remotes. Before the last one gave up the ghost, [Steve] captured the IR codes for each button using an Arduino and the IRRemote library. With codes in hand, it was pretty straightforward to get the Nano to send them with an IR LED. But what makes this project unique is that the custom GUI that controls the Arduino was written in the language that everyone loves to hate, Visual Basic. It’s a dirty little secret that lots of corporate shops still depend on VB, and it’s good to see a little love for the much-maligned language for a change. Plus it got the job done.
Want to dive deeper into IR? Maybe this primer on cloning IR remotes with an Arduino will help. And for another project where VB shines, check out this voice controlled RGB LED lamp.
Propane Tanks Transformed Into Extreme Sandblaster
The [Make It Extreme] team has been racking up the builds lately, and a lot of them are heavy with metalworking. When you’re doing that kind of work, and you put as much care into finishing your builds like they do, it’s a good idea to have access to a sandblaster. So naturally, they built a really nice one.
We’ve featured a couple of [Michalis Mavros] and team’s build recently; you’ll no doubt recall this viciously effective looking spot welder and a sketchy angle grinder cum belt sander. The sandblaster build, centered as it is around scrap propane tanks, has some lethal potential, but luckily the team displaced any remaining gas from the tanks with water before doing any cutting. The design allows for a lot of sand in the tanks, with plans to provide a recycling system for the grit, which is a nice touch. And it works great – they even used it to clean it up before final finishing in the trademark [Make It Extreme] green and black paint job.
What we really like about the video, though, is that it’s a high-speed lesson on metalworking techniques. There’s a ton to learn here about all the little tricks needed to bring a large-scale metalworking project to fruition. It also demonstrates that we really, truly need a plasma cutter and a metalworking lathe.
Continue reading “Propane Tanks Transformed Into Extreme Sandblaster”
Custom Case Lends Retro Look To Smart TV
Refits of retro TVs and radios with the latest smart guts are a dime a dozen around Hackaday. And while a lot of these projects show a great deal of skill and respect for the original device, there’s something slightly sacrilegious about gutting an appliance that someone shelled out a huge portion of their paycheck to buy in the middle of the last century. That’s why this all-new retro-style case for a smart TV makes us smile.
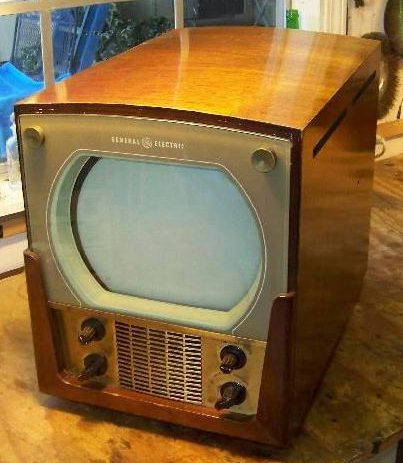
Another reason to smile is the attention to detail paid by [ThrowingChicken]. His inspiration came from a GE 806 TV from the 1940s, and while his build isn’t an exact replica, we think he captured the spirit of the original perfectly. From the curved top to the deep rectangular bezel, the details really make this a special build. One may quibble about not using brass for the grille like the original and going with oak rather than mahogany. In the end though, you need to work with the materials and tooling you have. Besides, we think the laser cut birch ply grille is pretty snazzy. Don’t forget the pressure-formed acrylic dome over the screen – here’s hoping that our recent piece on pressure-forming helped inspire that nice little touch.
This project was clearly a labor of love – witness the bloodshed after a tangle with a tablesaw while building the matching remote – and brought some life to an otherwise soulless chunk of mass-produced electronics.
[via r/DIY]
Solving ISP Problem With A Homebrew LTE Yagi
We’ve heard reports that internet connectivity in Australia can be an iffy proposition, and [deandob] seems to back that up. At the limit of a decent DSL connection and on the fringe of LTE, [deandob] decided to optimize the wireless connection with this homebrew Yagi antenna.
Officially known as the Yagi-Uda after its two Japanese inventors from the 1920s, but generally shortened to the name of its less involved but quicker to patent inventor, the Yagi is an antenna that provides high gain in one direction. That a homebrew antenna was even necessary at all is due to [deandob]’s ISP using the 2300MHz band rather than the more popular 2400MHz – plenty of cheap 2.4GHz antennas out there, but not so much with 2.3GHz. With multiple parallel and precisely sized and spaced parasitic elements, a Yagi can be a complicated design, but luckily for [deandob] the ham radio community has a good selection of Yagi design tools available. His final design uses an aluminum rod for a boom, 2mm steel wire for reflectors and directors, and a length of coax as the driven element. The result? Better connectivity that pushes his ISP throttling limit, and no more need to mount the modem high enough in his house to use the internal antenna.
People on the fringes of internet coverage go to great lengths to get connections, like this off-grid network bridge. Or if you’d rather use a homebrew Yagi to listen to meteors, that’s possible too.
To See Within: Making Medical X-rays
I was a bit of a lost soul after high school. I dabbled with electrical engineering for a semester but decided that it wasn’t for me – what I wouldn’t give for a do-over on that one. In my search for a way to make money, I stumbled upon radiologic technology – learning how to take X-rays. I figured it was a good way to combine my interests in medicine, electronics, and photography, so after a two-year course of study I got my Associates Degree, passed my boards, and earned the right to put “R.T.(R) (ARRT)” after my name.
That was about as far as that career went. There are certain realities of being in the health care business, and chief among them is that you really have to like dealing with the patients. I found that I liked the technology much more than the people, so I quickly moved on to bigger and better things. But the love of the technology never went away, so I thought I’d take a look at exactly what it takes to produce medical X-rays, and see how it’s changed from my time in the Radiology Department.
That’s No Moon – That’s A Bamboo Death Star
At first glance, [Frank Howarth]’s turned bamboo Death Star seems like a straight woodworking project. No Arduino controlled lights, no Raspberry Pi for audio clips of an X-wing attack or escaping TIE fighter. In other words: where’s the hack?
It’s a freaking bamboo Death Star!
If that’s not enough for you, check out the pattern on the surface of the finished model. That’s not painted on – those are the layers of the laminated bamboo lumber used to create the rings [Frank] used to form the structure. After lots of turning, sanding and polishing, the characteristic vascular bundles of the bamboo create light and dark panels for a convincing effect of the Death Star’s surface detail. And although we like the natural finish, we can imagine a darker stain might have really made the details pop and made for an effect closer to the original.
Still not hackish enough? Then feast your eyes on [Frank]’s shop. It’s a cavernous space with high ceilings, tons of natural light, and seemingly every woodworking machine known to man. While the lathe and tablesaw do a lot of the work for this build, the drool-worthy CNC router sees important duty in the creation of the multiple jigs needed for the build, and for making the cutout for the superlaser, in what must have been a tense moment.
Bamboo is an incredible material, whether for fun builds like this or for more structural uses, like a bamboo bike. All this bamboo goodness puts us in the mood to call on [Gerrit Coetzee] for a new installment on his “Materials You Should Know” series.
Continue reading “That’s No Moon – That’s A Bamboo Death Star”