There are so many ways to make things look awesome by pulling inspiration from great retro hardware. And combining today’s futuristic functionality with yesterday’s lines, colors, and kitsch is the quick path to a winning combination. So why not give it a try and show us what you got? That’s the gist of Hackaday’s Reinvented Retro Contest which begins right now and runs through June.
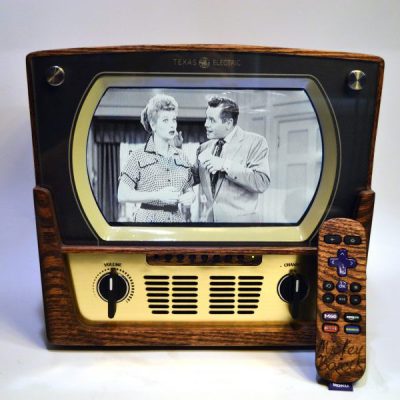
This smart TV should help get you thinking in a retro-modern way. You’d never know it wasn’t stock… except when it starts streaming The Falcon and the Winter Soldier via the Roku hidden inside. Fit and finish on this one is spectacular and that woodgrain remote is a piece of artwork!
So what will it be? Keurig in a 1960’s Perculator? Desk lamp in a rotary telephone? GHz oscilloscope where a CRT used to live? Perhaps a Raspberry Pi laptop in a 1990’s form-factor? You get to decide what “Retro” means, just make sure you thoroughly show off the build!
Digi-Key is sponsoring this contest and there are $200 shopping sprees from their warehouse up for grabs for each of three top winners. Make a project page over on Hackaday.io and use the “Submit project to…” dropdown in the left side bar to enter it in the Reinventing Retro Contest.