The humble automotive alternator hides an interesting secret. Known as the part that converts power from internal combustion into the electricity needed to run everything else, they can also themselves be used as an electric motor.
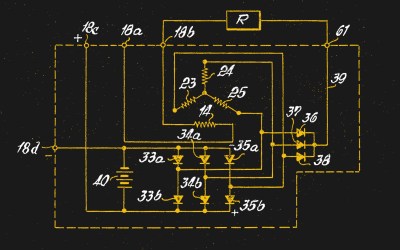
These devices almost always take the form of a 3-phase alternator with the magnetic component supplied by an electromagnet on the rotor, and come with a rectifier and regulator pack to convert the higher AC voltage to 12V for the car electrical systems. Internally they have three connections to the stator coils which appear to be universally wired in a delta configuration, and a pair of connections to a set of brushes supplying the rotor coils through a set of slip rings. They have a surprisingly high capacity, and estimates put their capabilities as motors in the several horsepower. Best of all they are readily available second-hand and also surprisingly cheap, the Ford Focus unit shown here came from an eBay car breaker and cost only £15 (about $20).
We already hear you shouting “Why?!” at your magical internet device as you read this. Let’s jump into that.
Continue reading “Car Alternators Make Great Electric Motors; Here’s How”