Underwater robots face many challenges, not least of which is how to move around. ZodiAq is a prototype underwater soft robot (link is to research paper) that takes an unusual approach to this problem: multiple flexible appendages. The result is a pretty unconventional-looking device that can not only get around effectively, but can do so without disturbing marine life.
ZodiAq sports a soft flexible appendage from each of its twelve faces, but they aren’t articulated like you might think. Despite this, the device can crawl and swim.
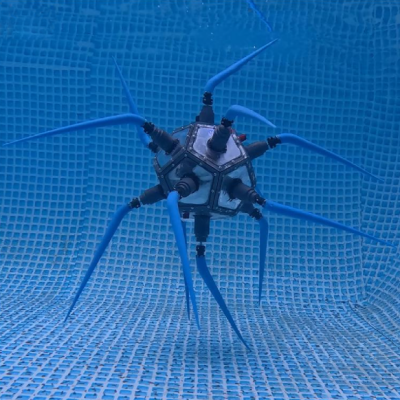
Each soft appendage is connected to a motor, which rotates the attached appendage. This low-frequency but high-torque rotation, combined with the fact that each appendage has a 45° bend to it, has each acting as a rotor. Rotation of the appendages acts on the surrounding fluid, generating thrust. When used together in the right way, these appendages allow the unit to move in a perfectly controllable manner.
This locomotion method is directly inspired by the swimming gait of bacterial flagella, which the paper mentions are regarded as the only example of a biological “wheel”.
How fast can it go? The prototype covers a distance of two body lengths every fifteen seconds. True, it’s no speed demon compared to a propeller, but it doesn’t disturb marine life or environments as it moves around. This method of movement has a lot going for it. It’s adaptable and doesn’t use all twelve appendages at once; so there’s redundancy built in. If some get damaged or go missing, it can still move, just slower.
ZodiAq‘s design strikes us as a very accessible concept, should any aspiring marine robot hackers wish to give it a shot. We’ve seen other highly innovative and beautiful underwater designs as well, like body-length undulating fins and articulated soft arms.
We do notice that since it lacks a “front” — it might be a challenge to decide how to mount something like a camera. If you have any ideas, share them in the comments.