As a recent emigre from the Ubuntu Linux distribution to Manjaro, I’ve had the chance to survey the field as I chose a new distro, and I realised that there’s a whole world of operating systems out there that we all know about, but which few of us really know. Hence this is the start of what I hope will be a long-running series, in which I try different operating systems in my everyday life as a Hackaday writer, to find out about them and then to see whether they can deliver on the promise of giving me a stable platform on which to earn a living.
For that they need an internet connection and a web browser up-to-date enough to author Hackaday stories, as well as a decent graphics package. In addition to using the OS every day though, I’ll also be taking a look at what makes it different from all the others, what its direction and history is, and how user-friendly it is as an experience. Historical systems such as CP/M are probably out of the question as are extremely esoteric ones such as the famous TempleOS, but this still leaves plenty of choice for an operating system tourist. Join me then, as I try all the operating systems.
A Distro From The 1990s, Today
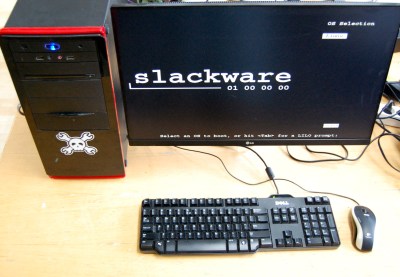
When deciding where to start on this road, there was an obvious choice. Slackware was the first Linux-based distribution I tried back in 1995, I’m not sure which version it was , but it came to me via a magazine coverdisk. It was by no means the first OS that captured my attention as I’d been an Amiga user for quite a few years at that point, but at the moment I can’t start with AmigaOS as I don’t have nay up-to-date Amiga-compatible hardware.
July 2023 also marks the 30th anniversary for the distro making it the oldest one still in active development, so this seems the perfect month to start this series with the descendant of my first Linux distro. Slackware 15 comes as a 3.8 GB ISO file download for 64-bit computers, and my target for the distro was an old desktop PC with an AMD processor and a big-enough spinning rust hard disk which had been a high-end gaming system a little over ten years ago. Not the powerhouse it once was, but it cost me nothing and it’s adequate for my needs. Installed on a USB Flash drive the Slackware installer booted, and I was ready to go. Continue reading “Jenny’s Daily Drivers: Slackware 15”