If you’ve been on the Internet long enough to know about Hackaday, we’ll wager you’re familiar with the concept of autonomous sensory meridian response (ASMR) — a tingling sensation in the scalp that’s said to be triggered by certain auditory stimuli. There are countless videos on YouTube that promise to give you “the tingles” using everything from feather dusters to overly starched shirts, but for us, the tool of choice is apparently a Lincoln Electric Magnum PRO 100SG spool gun in the hands of [Bob].
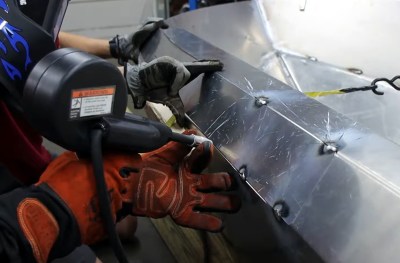
Admittedly we can’t promise the latest Making Stuff video will induce a euphoric physical sensation for all viewers, but at the very least, we think you’ll agree that watching [Bob] and his brother methodically welding together the twelve foot hull of what will eventually be a custom jet boat is strangely relaxing.
While we usually associate [Bob] with scratch builds, this time he’s actually working his way through a commercial kit. Sold by Jet Stream Adventure Boats, the kit includes the pre-cut aluminum panels that make up the hull, stringers, and top deck — niceties like a windshield and seats are offered as extras. The engine and jet drive need to be salvaged from an existing personal watercraft (PWC), but that will have to wait for a future video. For now, there’s a boat-load (get it?) of tack welding to be done.
The build process looks to go pretty smoothly, except for when they attempt to put the bow of the boat together. Unable to get the two side panels to meet properly, [Bob] eventually has to contact the manufacturer. After some back and forth, it turns out that a bit must have broken on the CNC when the hull panel went through, as a key cut was made nearly 8 inches (20 cm) too short. He was able to complete the cut with a jigsaw and continue on with the build, but we’re still scratching our heads at how this wasn’t caught before it got shipped out.
It won’t be the first homemade boat we’ve covered, but given [Bob]’s attention to detail, we’re particularly excited to see how this one develops in future videos. Especially since he’s foolishly bravely asked the commenters to come up with a name for his new craft.
Continue reading “Watching A Boat Get Welded Together Is Workshop ASMR”