Hackaday started off Thursday of the Consumer Electronics Show with an impromptu breakfast meetup. This turns out to be a wonderful thing as it lets you ease into a 16 hour day of standing, walking, talking, and getting lost trying to find your way from conference hall to conference hall. We had a great turnout and many brought their hacks and demos to show off. A big thanks to the Sambalatte staff who are awesome people and top tier baristas.
CastAR
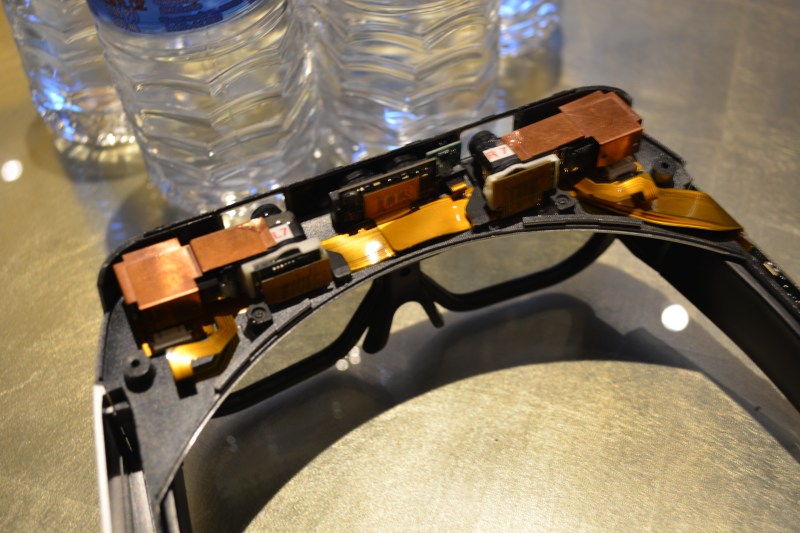
Before leaving for CES I was talking to [Ben Krasnow] about what we should try to see and he suggested looking for private showings that are given in the suites of the hotels at the conference. Turns out our friends at Technical Illusions are doing just that. [Jeri] and [Rick] were showing off CastAR in a suite during the week and were nice enough to make room in their booked schedule for a private Demo.
What you see above are the guts of the version they are currently shipping as part of their Kickstarter fulfillment. I also got a look at a rev2 prototype and will write a follow-up post with more information on the whole experience when I have more time.
Eureka, Startups!
There is a loop of aisles in the Sands that has startup booths and most of the interesting things I saw on Wednesday and Thursday are there. Here we have a jamming gripper robot arm. It’s designed for things like moving oddly shaped goods on a manufacturing line. Empire Robotics hit a homerun with their demo for the booth, a take on beer-bong: robot versus human. The scoreboard showed the robot winning an order of magnitude more than the humans.
[Todd] was at was at the Tinkerines booth showing off 3D printers aimed to augmented the STEM curriculum. We couldn’t help but notice his TIE fighter right and inquired about it. He modeled the design himself, send it off to be cast in silver, and inlaid the stone when the ring came back from the casting service. Sweet!
LVBots
[Sarah Petkus] clued me in and gave me a ride to the Pololu CES open house. The night coincided with the LVBots meetup which they support by providing space for the meetings. There were lots of cool robots being shown off. What you see here was just the pre-meeting warmup of line-followers and sumo robots. I shot some video of the show-and-tell which we’ll post once we’ve had a chance to edit the content.
Closing out CES
Today is the last day of the conference. I stopped by the Voltera PCB printer booth yesterday but they were nowhere to be found. Turns out they were being handed a $50k check by TechCrunch for winning the Battleground. I suppose we’ll give them a pass for not being at the table during that!
I’ll be headed over this afternoon to catch up with them. I’m also hoping to get a look at the Voxel8 printer. If you have any other “can’t-miss” suggestions let me know in the comments and I’ll try to add them to my CES dance card.