[Peter Holderith] set out some time ago to build an electric go-kart. That by itself is not terribly unusual, but where his project diverts from the usual is in the fact that each of the four wheels has an integrated hub motor.
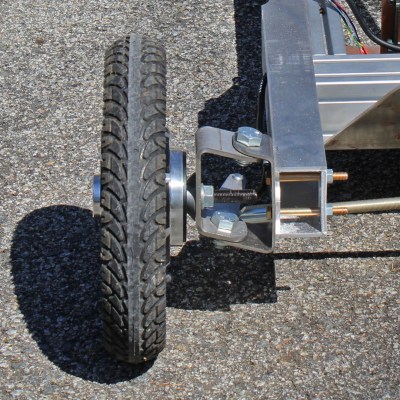
This kart project is a bit of a work in progress, with [Peter] previously building (then scrapping) a failed attempt at a cheap suspension system. But it’s completely operational with all four wheels able to deliver a monstrous amount of power despite being limited by the power supply (a battery pack salvaged from an Audi Q5 Hybrid).
The kart might not look it, but it weighs 177 pounds (80 kg) with the battery and motors accounting for nearly half of that. What is is like to drive? “Nothing short of thrilling,” says [Peter]. It’s got no suspension and is pretty bare bones, not to mention limited in power by the battery, but [Peter] finds it a satisfying drive that nevertheless delivers car-like cues in the driving experience. The build isn’t done, and [Peter] plans to see if more power is available by switching battery chemistries rather than add more battery weight.
Building and driving electric vehicles can be remarkably satisfying, and it’s an area in which hobbyists can meaningfully innovate. Self-balancing one-wheeled vehicles for example look like a ton of fun. Heck, researchers have discovered that even rats seem to enjoy driving just for the fun of it.