Korean researchers have created a very realistic and capable robot hand that looks very promising. It is strong (34N of grip strength) and reasonably lightweight (1.1 kg), too. There are several videos of the hand in action, of which you can see two of them below including one where the hand uses scissors to cut some paper. You can also read the full paper for details.
Robots Hacks2349 Articles
OpenDog Version 3 Is Ready To Go Walkies
We’ve been following [James Bruton]’s open dog project for a little while now, and with his considerable pace of work – pandemic or no pandemic – development has been incredibly rapid. The latest milestone is the public release of version 3 (Video, embedded below.) This upgrade to the system adds 3D printed cycloidal gearboxes, removing the previous belt drives. [James] had immense fun tuning the motor controller parameters for these and admits they’re not completely dialed in yet. He notes that the wider gearbox body means that the robots geometry needed to change a little, and the previous belt-drive version may have a bit of an edge, but he’s confident he can make it work (and given his incredible previous robotics builds, we totally believe he’ll nail it!)
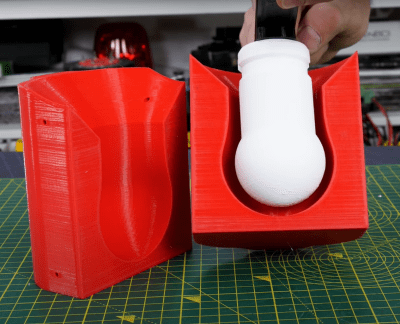
Older versions struggled with slippery plastic feet; the advantage of a predictably smooth contact shape of a rounded foot is somewhat offset by the limited contact patch size, and that means not so much grip on some surfaces. [James] solution was obvious enough – just learn how to make 3D printed silicone moulds and cast a nice rubber foot around a plastic former, and problem solved! Unfortunately he neglected to add some recesses for a lever to get in between the mould halves, so it was a bit of a struggle to separate after curing. A beginner’s mistake that won’t be repeated, we’re sure.
Full source for openDogV3 is now available on the GitHub page. Here’s the playlist for the whole project, as well as direct links for the cycloidal drive development (part1, part2, part3.) But before you all go diving in to start 3D printing your own pooch, [James] tells us that the total cost would be around $2000 all in, with the bulk of that being the motors and ODrive units, so this one for the serious builder only!
We’ve covered robot dogs a fair bit, a particularly nice example is The Dizzy Wolf, and if you’re wondering just why on earth you’d want a robot dog, then Ask Hackaday has you covered as well.
A Self Righting Balancing Robot Configured The Easy Way
Norwegian electronics hacker [Hans Jørgen] aka [time expander] on YouTube, has a clear interest in robotics, and for his latest effort, decided that it was time to build a custom controller platform. Since [Hans] had a pile of Dynamixel servo motors lying around to test it with, a good first project for the platform was a simple self-balancing wheeled robot. (Video, embedded below)
We say ‘simple’ but that isn’t really the case, as there is a fair bit going on to get this to work. The first problem, is sensing, which was quickly solved with the excellent BMO055 IMU chip. Next, what to do when it falls over? Simply adding some servo-controlled arms, allowed the robot to flip itself back upright. Control is covered with a ESP32-WROOM-32D module from our friends at Espressif, which enables remote firmware uploading over the air (OTA update) as well as parameter tuning. In order to implement the latter, [Hans] chose to use bonjour/mDNS which is an implementation of zero-configuration networking. This gets the ESP32 onto the WiFi, but it isn’t immediately obvious how to connect to it, without a little digging around. To simply connection, [Hans] implemented a dynamic QR code via the connected OLED. This is just one of the those tiny 0.96″ displays that you see touted all over our corners of the internet.
Simply by scanning the QR code with any compatible device to hand brings up a simple configuration web page, allowing one to tweak the PID controller parameters, and get that balancing robot into check. Great stuff!
The PCB was designed in Eagle, firmware for the ESP32 is available, 3D models for the plastic are designed with fusion 360, and [Hans] is even currently working on some preliminary Alexa integration. What a fun project!
All the above, albeit an early cut (look out for bugs!) is available on the project GitHub for your viewing pleasure.
We’re no stranger to self-balancing 3D-printed bots, whilst you’re here, why not checkout A problematic Self-Balancing Sonic the Hedgehog? If wheeled bots aren’t your cup-of-tea, there’s a not-at-all freaky one-legged bouncing bot that may be of interest.
Continue reading “A Self Righting Balancing Robot Configured The Easy Way”
Squishy Robot Hardware Does Well Under Pressure
If your jealousy for Festo robots is festering, fret not! [mikey77] has shown us that, even without giant piggy banks, we can still construct some fantastic soft robotics projects with a 3D printer and a visit to the hardware store. To get started, simply step through the process with this 3D Printed Artificial Muscles: Erector Set project on Instructables.
In a nutshell, [mikey77] generously offers us a system for designing soft robots built around a base joint mechanism: the Omega Muscle. Fashioned after its namesake, this base unit contains an inflatable membrane that expands with pressure and works in tandem with another Omega Muscle to produce upward and downward angular movement. Each muscle also contains two endpoints to connect to a base, a gripper, or more Omega Muscles. Simply scale them as needed and stack them to produce a custom soft robot limb, or use the existing STLs to make an articulated soft gripper.
This project actually comes in two parts for robot brawns and brains. Not only does [mikey77] take us through the process for making Omega muscles, we also get a guide for building the pressure system designed to control them. Taken together, it’s a feature-complete setup for exploring your own soft robotics projects with a great starting project. Stay tuned after the break for a demo video in action. There’s no audio, but we’re sure you’ll be letting off an audible pssssh in satisfaction to follow along.
It’s not every day that we see FFF-based 3D printers making parts that need to be airtight. And [mikey77’s] success has us optimistic for seeing more air muscles in future projects down the road. In the meantime, have a look at the silicone-silicon half-breeds that we’ve previously caught pumping iron.
Continue reading “Squishy Robot Hardware Does Well Under Pressure”
Wake-Up Robot Does It Gently
For hundreds of years, people have fallen asleep while reading in bed late at night. These days it’s worse, what with us taking phones to the face instead when we start to nod off. At least they don’t have pointy corners like books. While you may not want to share your bedroom with a robot, this wake-up robot by [Norbert Zare] may be just the thing to keep you awake.
Here’s how it works: a Raspberry Pi camera on a servo wanders around at eye level, and the Pi it’s attached to uses OpenCV to determine whether those eyes are open or starting to get heavy. The bot can also speak — it uses eSpeak to introduce itself as a bot designed not to let you sleep. Then when it catches you snoozing, it repeatedly intones ‘wake up’ in a bored British accent.
We were sure that the thing was designed to slap [Norbert] in the face a la [Simone Giertz]’s robot alarm clock, but no, that long-fingered hand just slowly swings down and gently taps [Norbert] on the arm (or whatever is in the path of the slappy hand). Check out the short demo and build video after the break.
Do you want to be awoken even more gently? Try a sunlight lamp. We’ve got dozens in stock, but this one gradually gets about as bright as the sun.
It’s Nice Having Someone To Talk To
We all get a bit lonely from time to time and talking to other humans can be a challenge. With social robots still finding their way these days, [Markus] decided to find a DIY solution he could make cheaply, resulting in the “Conversation Face.”
The build is actually pretty simple, really. You have three different OLED displays, two for the eyes and one for the mouth, that have different graphic images programmed onto them depending on the expression being displayed. There’s also a small electret microphone that senses when you are speaking to the face. Finally, a simple face cutout covers the electronics and solidifies the aesthetic.
The eyes are programmed identically since they would move together for most expressions. [Markus] was able to get a blinking animation by quickly moving a white circle vertically through the eye screens and the results are pretty convincing. He also moves the eyes around the OLED to make the expressions seem more dynamic.
There’s not much to the mouth. [Markus] only has a mouth open and a mouth closed animation. The mouth opens when it’s the face’s turn to talk or closes when the face should be listening. This information is easily determined by measuring the output of the microphone. Interestingly enough, you can program the face to be quiet and attentive when it’s being spoken to or quite chatty to show that it’s actively engaging in the conversation.
I don’t know about you, but we can’t decide if the Conversation Face is more or less creepy than those social robots. Either way, we thought you would get a kick out of it regardless. It also looks like a funny anime character if you ask us.
Light-Tracking BEAM Robot Can See The Light
BEAM robotics, which stands for Biology, Electronics, Aesthetics, and Mechanics, is an ethos that focuses on building robots with simple analog circuits. [NanoRobotGeek] built a great example of the form, creating a light-tracking robot that uses no batteries and no microcontrollers.
The robot aims to track the brightest source of light it can see. This is achieved by feeding signals from four photodiodes into some analog logic, which then spits out voltages to the two motors that aim the robot, guiding it towards the light. There’s also a sound-detection circuit, which prompts the robot to wiggle when it detects a whistle via an attached microphone.
The entire circuitry is free-formed using brass wire, and the result is an incredibly artful build. Displayed in a bell jar, the build looks like some delicate artifact blending the past and future. Neither steampunk nor cyberpunk, it draws from both with its combination of vintage brass and modern LEDs.
It’s a great build that reminds us of some of the great circuit sculptures we’ve seen lately. Video after the break.
Continue reading “Light-Tracking BEAM Robot Can See The Light”