Let’s think of the last time you sent data without wires. We’re not talking WiFi here, but plain optical signals. Free-space optical communication, or FSO, is an interesting and easy way to transmit signals through light beams. Forget expensive lasers or commercial-grade equipment; this video by [W1VLF] offers a simple and cheap entry point for anyone with a curiosity for DIY tech. Inspired by a video on weak signal sources for optical experiments, this project uses everyday components like a TV remote-control infrared LED and a photo diode. The goal is simply to establish optical communication across distances for under $10. Continue reading “Beam Me Up: Simple Free-Space Optical Communication”
beam27 Articles
Makerpipe Turns Conduit Into Structures
At the risk of stating the obvious, building big things can be difficult. Sure, parts that fit on the bed of a 3D printer are easy to make, if not particularly fast, and scaling up from there is possible. But if you need a long beam or structural element, printing makes little sense; better to buy than build in that case. The trouble then becomes, how do you attach such parts together?
Enter Makerpipe. This South Carolina company, recently out of a crowdfunding campaign, makes a range of structural connectors and fittings for electrical mechanical tubing, or EMT, the galvanized steel conduit used in the electrical trades. EMT is widely available in multiple sizes and is relatively cheap, although we have noticed that the price here has ticked up quite a bit over the last couple of years. It also has the advantage of being available off-the-shelf at any big-box home improvement store, meaning you have instant access to a fantastic building material.
Makerpipe’s bolt-together couplings let you turn pieces of EMT, easily cut with a hacksaw or pipe cutter, into structures without the need for welding. Yes, you can do the same with extruded aluminum, but even if you’re lucky enough to live near a supply house that carries extrusions and the necessary fittings and is open on Saturday afternoon, you’ll probably pay through the nose for it.
Makerpipe isn’t giving their stuff away, and while we normally don’t like to feature strictly commercial products, something that makes building large structures easier and faster seems worth sharing with our community. We’ve done our share of fabricobbling together EMT structures after all, and would have killed for fittings like these.
One Object To Print, But So Many Settings!
When working with an FDM 3D printer your first prints are likely trinkets where strength is less relevant than surface quality. Later on when attempting more structural prints, the settings become very important, and quite frankly rather bewildering. A few attempts have been made over the years to determine in quantifiable terms, how these settings affect results and here is another such experiment, this time from Youtuber 3DPrinterAcademy looking specifically at the effect of wall count, infill density and the infill pattern upon the strength of a simple beam when subjected to a midpoint load.
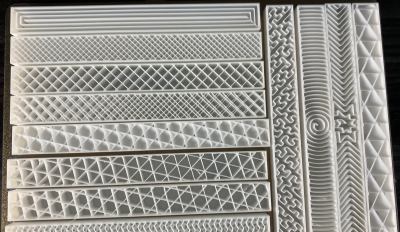
When setting up a print, many people will stick to the same few profiles, with a little variety in wall count and infill density, but generally keep things consistent. This works well, up to a point, and that point is when you want to print something significantly different in size, structure or function. The slicer software is usually very helpful in explaining the effect of tweaking the numbers upon how the print is formed, but not too great at explaining the result of this in real life, since it can’t know your application. As far as the slicer is concerned your object is a shape that will be turned into slices, internal spaces, outlines and support structures. It doesn’t know whether you’re making a keyfob or a bearing holder, and cannot help you get the settings right for each application. Perhaps upcoming AI applications will be trained upon all these experimental results and be fed back into the slicing software, but for now, we’ll just have to go with experience and experiment. Continue reading “One Object To Print, But So Many Settings!”
Printed Circuit Bird Family Calls For Us To Consider Analog
On our favourite low-attention-span content site, [Kelly Heaton] has recently started sharing a series of “Printed Circuit Birds”. These are PCBs shaped like birds, looking like birds and chirping like birds – and they are fully analog! The sound is produced by a network of oscillators feeding into each other, and, once tuned, is hardly distinguishable from the bird songs you might hear outside your window. Care and love was put into making this bird life-like – it perches on Kelly’s arm with legs woven out of single-strand wire and talons made out of THT resistors, in the exact same way you would expect a regular bird to sit on your arm – that is, if you ever get lucky enough. It’s not just one bird – there’s a family of circuit animals, including a goose, a crow and even a cricket.
Why did these animals came to life – metaphorically, but also, literally? There must be more to a non-ordinary project like this, and we asked Kelly about it. These birds are part of her project to explore models of consciousness in ways that we typically don’t employ. Our habit is to approach complex problems in digital domains, but we tend to miss out on elegance and simplicity that analog circuits are capable of. After all, even our conventional understanding of a neural network is a matrix of analog coefficients that we then tune, a primitive imitation of how we assume human brains to work – and it’s this “analog” approach that has lately moved us ever so closer to reproducing “intelligence” in a computer.
Kelly’s work takes a concept that would have many of us get the digital toolkit, and makes it wonderfully life-like using a small bouquet of simple parts. It’s a challenge to our beliefs and approaches, compelling in its grace, urging us to consider and respect analog circuits more when it comes to modelling consciousness and behaviours. If it’s this simple to model sounds and behaviour of a biological organism, a task that’d have us writing DSP and math code to replicate on a microcontroller – what else are we missing from our models?
Kelly has more PCBs to arrive soon in preparation for her NYC exhibit in February, and will surely be posting updates on her Twitter page! We’ve covered her work before, and if you haven’t seen it yet, her Supercon 2019 talk on Electronic Naturalism would be a great place to start! Such projects tend to inspire fellow hackers to build other non-conventional projects, and this chirping pendant follows closely in Kelly’s footsteps! The direction of this venture reminds us a lot of BEAM robotics, which we’ve recently reminisced upon as something that’s impacted generations of hackers to look at electronics we create through an entirely different lens.
Continue reading “Printed Circuit Bird Family Calls For Us To Consider Analog”
BEAM Bird Pendant Really Chirps
[NanoRobotGeek] had a single glorious weekend between the end of the term and the start of exams. Did they buy a keg and party it up? No, in fact, quite the opposite — they probably gained a few brain cells by free-form soldering this beautiful chirping bird pendant at 0603 instead.
The circuit is a standard BEAM project built around a 74HC14, but [NanoRobotGeek] made a few changes to achieve the ideal chirp sound. As you can see in the video after the break, it chirps for around 30 seconds and then shuts off for 1-2 minutes before starting up again.
What is better than a BEAM project? A portable one, we say. Although the chirping would probably get old pretty quickly, there’s just no substitute for working so small that you can carry it around your neck and show it off.
This one is kind of a long time coming, because [NanoRobotGeek] started by breadboarding the circuit and then made a PCB version way back in 2019, which they were attempting to miniaturize with this project. We think they did a fantastic job of it, and the documentation is stellar if you are crazy enough to attempt this one. You will need a lot of blu tack and patience, and pre-tinning is your friend. Be sure to check out the demo after the break.
The name checks out, and this isn’t [NanoRobotGeek]’s first foray into tiny circuit sculpture — just take a look at all we’ve covered.
Hackaday Podcast 146: Dueling Trackballs, Next Level BEAM Robot, Take Control Of Your Bench, And Green Programming
Postpone your holiday shopping and spend some quality time with editors Mike Szczys and Elliot Williams as they sift through the week in Hackaday. Which programming language is the greenest? How many trackballs can a mouse possibly have? And can a Bluetooth dongle run DOOM? Join us to find out!
Take a look at the links below if you want to follow along, and as always, tell us what you think about this episode in the comments!
Direct download (52 MB)
Light-Tracking BEAM Robot Can See The Light
BEAM robotics, which stands for Biology, Electronics, Aesthetics, and Mechanics, is an ethos that focuses on building robots with simple analog circuits. [NanoRobotGeek] built a great example of the form, creating a light-tracking robot that uses no batteries and no microcontrollers.
The robot aims to track the brightest source of light it can see. This is achieved by feeding signals from four photodiodes into some analog logic, which then spits out voltages to the two motors that aim the robot, guiding it towards the light. There’s also a sound-detection circuit, which prompts the robot to wiggle when it detects a whistle via an attached microphone.
The entire circuitry is free-formed using brass wire, and the result is an incredibly artful build. Displayed in a bell jar, the build looks like some delicate artifact blending the past and future. Neither steampunk nor cyberpunk, it draws from both with its combination of vintage brass and modern LEDs.
It’s a great build that reminds us of some of the great circuit sculptures we’ve seen lately. Video after the break.
Continue reading “Light-Tracking BEAM Robot Can See The Light”