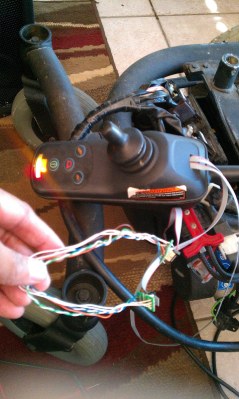
Building robots can be fun, and remains a popular pastime among many in the hacker and maker set. However the hardware side of things can be daunting. This is particularly the case for those attempting to build something on a larger scale. A great shortcut is to start with a robust mechanical platform from the outset – and using an electric wheelchair is a great way to do so.
[Nikita] started this project way back in 2009, after finding a broken electric wheelchair at a flea market. It was no longer in fit condition for use as a wheelchair, so [Nikita] was able to score it for the low price of just $50. That’s a great price for a package which includes a robust chassis, wheels, motors and the required controllers to drive it all. With the platform in hand, it was time to get hacking.
Thus far, [Nikita] has gone so far as to strip the wheelchair of all extraneous parts, leaving it as a motorized carriage. Radio control has been implemented with the help of an Arduino, and a couple of “eyes” have been added to give it a little personality. It can also still be driven with the original joystick, which has been relocated on the chassis. Future plans involve adding a level of autonomy to allow the ‘bot to navigate waypoints and recognise faces, both tasks which should be significantly easier with 2019 technology. We’re eager to see where it goes next; we’ve seen great applications of wheelchair hardware before, after all. Video after the break.
Continue reading “Electric Wheelchair Makes A Great Base For A Big Robot”