Battlelines are being drawn in Canada over the lowly Flipper Zero, a device seen by some as an existential threat to motor vehicle owners across the Great White North. The story started a month or so ago, when someone in the government floated the idea of banning devices that could be “used to steal vehicles by copying the wireless signals for remote keyless entry.” The Flipper Zero was singled out as an example of such a nefarious device, even though relatively few vehicles on the road today can be boosted using the simple replay attack that a Flipper is capable of, and the ones that are vulnerable to this attack aren’t all that desirable — apologies to the 1993 Camry, of course. With that threat hanging in the air, the folks over at Flipper Devices started a Change.org petition to educate people about the misperceptions surrounding the Flipper Zero’s capabilities, and to urge the Canadian government to reconsider their position on devices intended to explore the RF spectrum. That last bit is important, since transmit-capable SDR devices like the HackRF could fall afoul of a broad interpretation of the proposed ban; heck, even a receive-only SDR dongle might be construed as a restricted device. We’re generally not much for petitions, but this case might represent an exception. “First they came for the Flipper Zero, but I did nothing because I don’t have a Flipper Zero…”
car240 Articles
New Brains Save 12 V Fridge From The Scrap Heap
Recently [nibbler]’s Evakool 55L vehicle fridge started to act strangely, reporting crazy temperature errors and had no chance of regulating. The determination was that the NTC thermistor was toast, and rather than trying to extricate and replace this part, it was a lot easier to add a new one at a suitable location
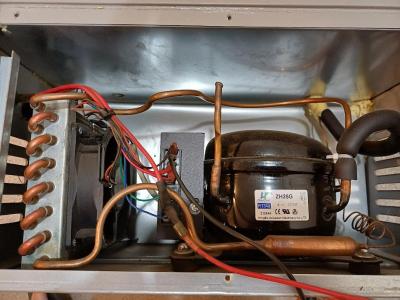
A straight swap would have been boring, so this was a perfect excuse for an overboard hack. Reverse engineering the controller wouldn’t be easy, as the data wasn’t available, as is often the case for many products of this nature.
While doing a brain transplant, the hacker way, we can go overboard and add the basics of an IoT control and monitoring system. To that end, [nibbler] learned as much as possible about the off-the-shelf ZH25G compressor and the associated compressor control board. The aim was to junk the original user interface/control board and replace that with a Raspberry Pi Pico W running CircuitPython.
For the display, they used one of the ubiquitous SH1106 monochrome OLED units that can be had for less than the cost of a McDonald’s cheeseburger at the usual purveyors of cheap Chinese electronics. A brief distraction was trying to use a DS18B20 waterproof thermometer probe, which they discovered didn’t function, so they reverted to tried and trusted tech — a simple NTC thermistor.
Continue reading “New Brains Save 12 V Fridge From The Scrap Heap”
Old Prius Gets Upgraded Batteries
So many of the batteries made today are lithium batteries of some sort, from mobile phones, laptops, and drones to electric cars and grid storage solutions. But this technology is relatively new; even as late as the 90s and early 00s the only widely-available batteries for things like power tools or the new hybrid vehicles coming on the market were nickel-metal hydride (NiMH). While it was good for the time, they don’t hold up to all of the advantages lithium has. There’s still plenty of hybrid vehicles on the road using these batteries, so if you’re driving an older Prius and want to give it a modern refresh, there’s a quick option to swap your old batteries.
Despite lithium technology being available for several decades, the switch to lithium for the Toyota Prius wasn’t instant, with many variants still using NiMH batteries as late as the 2020s largely because the NiMH batteries are less expensive and less maintenance-intensive than lithium batteries are. As these batteries lose capacity, the cars are still driveable but the advantages of the hybrid drivetrain won’t be as accessible anymore. The upgrade, from a company called Project Lithium, replaces these batteries with modern lithium technology that can improve the efficiency and performance of these cars even above their original capabilities since lithium batteries have more power density.
With the Toyota Prius being among the most reliable vehicles on the road thanks to the electric motor in the hybrid drivetrain taking a lot of stress off of the internal combustion engine, it’s often worth upgrading these old batteries to modern ones to squeeze every last mile from these workhorses as possible. With many of the replacement processes being almost as simple as lifting out an old battery and placing a new one in, it can be a no-brainer if that’s the only issue with the vehicle otherwise. This is also true of all-electric vehicles as well, although the process to replace the battery can be a little more involved.
Thanks to [JohnU] for the tip!
A 555 Can Even Make Your Car Indicator More Visible
Modern cars often come with white marker lights or daytime running lights that are on all the time, as a supplement to the primary headlights. The problem is that in some vehicle designs, these additional lights tend to make it harder to see the indicators when they’re on. [nibbler] had this very problem, and decided to solve it with a special interrupter circuit that cuts the daytime running light when the indicator is on. Even better, they used a 555 to do it!
The circuit is a simple monostable 555 circuit with an active low output. It’s triggered by the indicator signal. When the indicator is on, the circuit drives a relay to switch off the power to the daytime running light. Two copies of the circuit were built, one for the left side, and one for the right side of the car. This means that when the orange indicator is lit, it’s not being overwhelmed by the white daytime running light next to it. In fact, many automakers now program this behavior into their lighting by default.
It’s a nifty hack with a real positive safety impact. We’ve featured some other neat indicator hacks of late, like these tidy sequential indicators. Meanwhile, if you’re hacking on your own automotive lighting solutions, don’t hesitate to let us know!
ESP32 Used As Wireless CAN Bus Reader
The CAN bus, accessible through the OBD-II port, is the channel that holds all the secrets of the modern automobile. If you want to display those for your own perusal, you might consider this nifty tool from [EQMOD].
Yes, it’s an OBD-II dongle that you can build using an ESP32 WROVER module. It’s designed to read a car’s CAN bus communications and display them on a self-hosted web page, accessible over WiFi. The build relies on the dual-core nature of the ESP32, with the first core handling CAN bus duties via the SN65HVD230 CAN bus transceiver chip. The second core is responsible for hosting the web page. Data received via the CAN bus is pushed to the web user interface roughly every 60 to 100 milliseconds or so for information like RPM and speed. Less time-critical data, like temperatures and voltages, are updated every second.
It’s a neat little thing, and unlike a lot of dongles you might buy online, you don’t need to install some dodgy phone app to use it. You can just look at the ESP32’s web page for the data you seek. The graphics may be a little garish, but they do the job of telling you what’s going on inside your car. Plus, you can always update them yourself.
Getting to grips with the CAN bus is key if you want to diagnose or modify modern vehicles. Meanwhile, if you’ve been cooking up your own electronic vehicular hacks, don’t hesitate to drop us a line!
Hot Wheel Car Becomes 1/64 Scale Micro RC Car, Complete With Camera
If you enjoy watching skilled assembly of small mechanical systems with electronics to match, then make some time to watch [Max Imagination] transform a Hot Wheels car into a 1/64th scale RC car complete with video FPV video feed. To say the project took careful planning and assembly would be an understatement, and the results look great.
The sort of affordable electronics available to hobbyists today opens up all kinds of possibilities, but connecting up various integrated modules brings its own challenges. This is especially true when there are physical constraints such as fitting everything into an off-the-shelf 1/64 scale toy car.
There are a lot of interesting build details that [Max] showcases, such as rebuilding a tiny DC motor to have a longer shaft so that it can drive both wheels at once. We also liked the use of 0.2 mm thick nickel strips (intended for connecting cells in a battery pack) as compliant structural components.
There are actually two web servers being run on the car. One provides an interface for throttle and steering (here’s the code it uses), and the other takes care of the video feed with ESP32-CAM sending a motion jpeg stream. [Max]’s mobile phone is used to control the car, and a second device goes into an old phone-based VR headset to display the FPV video feed.
Circuit diagrams and code are available for anyone wanting to perhaps make a similar project. We’ve seen micro RC builds of high quality before, but integrating an FPV camera kicks things up a notch. Want even more complex builds? All the rules change when weight reduction is a non-negotiable #1 priority. Check out a micro RC plane that weighs under three grams and get a few new ideas.
Continue reading “Hot Wheel Car Becomes 1/64 Scale Micro RC Car, Complete With Camera”
Open Source Key Programmer For HiTag2 Keys
Hitag transponders have been used in a wide variety of car keys as a protective measure against hot-wiring and theft. They’re also a reason why it’s a lot more expensive to get car keys duplicated these days for many models that use this technology. However, there is now an open source programmer that works with these transponder keys, thanks to [Janne Kivijakola].
The hack uses an old reader device salvaged from a Renault in a scrapyard, hooked up to an Arduino Mega 2560 or Arduino Nano. With this setup, key transponders can be programmed via a tool called AESHitager, which runs on Windows. It’s compatible with a variety of Hitag transponders, including Hitag2, Hitag3, and Hitag AES, along with the VVDI Super Chip and certain types of BMW keys.
If you’ve been having issues with coded keys, this project might just be what you need to sort your car out. Everything you need is available on GitHub for those wishing to try this at home. We’ve seen some interesting hacks in this space before, too. Video after the break.
Continue reading “Open Source Key Programmer For HiTag2 Keys”