[Tallaustin] worked at Stratasys as an intern this past summer. They let him know that he was welcome to use their fancy industrial printers as much as he’d like. Not to waste such an opportunity he promptly got to work and designed an electric longboard, printable for a mere $8,000.
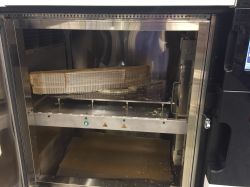
[Tallaustin] is presumably tall, and confided to Reddit that he weighs in at 210 lbs. For those of us who have had the pleasure of designing for FDM 3D printing, we know that getting a skateboard one can actually skate on without it delaminating somewhere unexpected is pretty difficult if you weigh 80 lbs, 200+ is another category entirely. So it’s not surprising that his first version shattered within in moments of testing.
So, he went back to the drawing board. Since he had his pick of all of Stratasys’s most expensive and fine spools of plastic, he picked one of the expensivest and finest, Ultem 1010. Aside from adding a lot of ribbing and plastic, he also gave it a full rundown with some of SolidWorks’s simulation tools to see if there were any obvious weak points.
Six days of exceedingly expensive printing later, he had a working long board. The base holds some batteries, an ESC, and a 2.4 GHz transceiver. The back has a brushless motor that drives a pulley slotted into one of the wheels. The rest is standard skateboard hardware.
If you’d like to build it yourself he’s posted the design on Thingiverse. He was even nice enough to put together a version that’s printable on a plebeian printer, for a hundredth of the price.