Way to rub it in, guys. As it turns out, due to family and work obligations we won’t be able to see the next Great American Eclipse, at least not from anywhere near the path of totality, when it sweeps from Mexico into Canada on April 8. And that’s too bad, because compared to the eclipse back in 2017, “Eclipse 2: Solar Boogaloo” is occurring during a much more active phase in the solar cycle, with the potential for some pretty exciting viewing. The sun regularly belches out gigatons of plasma during coronal mass ejections (CMEs), most of which we can’t see with the naked eye because not only is staring at the sun not a great idea, but most of that activity occurs across the disk of the sun, obscuring the view in the background light. But during the eclipse, we — oops, you — might just get lucky enough to have a solar prominence erupt along the limb of the sun that will be visible during totality. The sun has been quite active lately, as reflected by the relatively high sunspot number, so even though it’s an outside chance, it’s certainly more likely than it was in 2017. Good luck out there. Continue reading “Hackaday Links: March 24, 2024”
resin130 Articles
Multicolor Resin Prints: Give It A Shot
[Thomas TEMPE] has been making two-color resin prints. While printing in multiple colors is old hat for FDM printers, the way resin printers work makes it a more difficult proposition. [Thomas] has a simple solution. First, he prints an item with a cavity where he would like the second color. Then, after printing, he fills the cavity with a different color resin using a syringe and cures it. Simple, really.
Of course, it is all about technique. For fine lines, you’ll want a smaller needle, and you flood the area with the alternate resin and wipe away the excess. For wider lines, you simply fill the cavity from a larger syringe.
Make Carbon Fiber Tubes With An Open Source Filament Winder
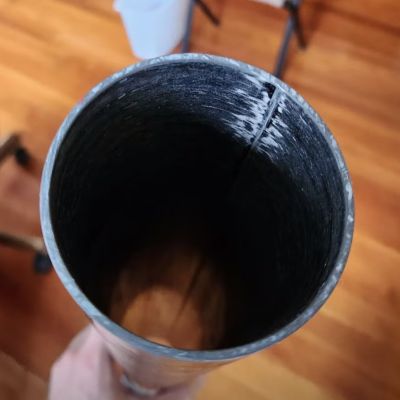
Carbon fiber (CF) is an amazing material that provides a lot of strength for very little weight, making it very useful for a lot of applications, ranging from rods in CoreXY 3D printers to model- and full-sized rockets. The model rocketry hobby is the reason why [Andrew Reilley] developed his own CF tube winding machine called Contraption. A tutorial video (also embedded below) shows how this machine is prepped for a winding run, followed by the winding progress and finalizing before admiring the result.
The entire machine’s design with 3D printed parts and off-the-shelf components is open source, as is the TypeScript and NodeJS-based Cyclone software that creates the toolpath specifying the parameters of the tube, including number of layers and the tow angle.
As a wet winding tow machine, the carbon fiber strands are led through the liquid resin before being wound onto the prepared mandrel. During winding some excess resin may have to be removed, and after the winding has been finished the tube is wound with shrink tape. This is followed by a heat gun session to shrink the tape and letting the resin cure. Following curing, the tape and mandrel are removed, resulting in a rather fancy looking CF tube that can find a loving home in a lot of applications, except perhaps ones that involving crushing outside pressures like those found deep below the ocean surface.
Continue reading “Make Carbon Fiber Tubes With An Open Source Filament Winder”
Retrotechtacular: The Story Of Turpentine
If someone in 2023 has ever had much call to use turpentine, chances are good it was something to do with paint or other wood finishes, like varnish. Natural turpentine is the traditional solvent of choice for oil paints, which have decreased in popularity with the rise of easy-to-clean polymer-based paints and coating. Oh sure, there are still those who prefer oil paint, especially for trim work — it lays up so nice — but by and large, turpentine seems like a relic from days gone by, like goose grease and castor oil.
It wasn’t always so, though. Turpentine used to be a very big deal indeed, as shown by this circa 1940 documentary on the turpentine harvesting and processing industry. Even then it was only a shadow of its former glory, when it was a vital part of a globe-spanning naval empire and a material of the utmost strategic importance. “Suwanee Pine” shows the methods used in the southern United States, where fast-growing pines offer up a resinous organic gloop in response to wounds in their bark. The process shown looks a lot like the harvesting process for natural latex, with slanting gashes or “catfaces” carved into the trunks of young trees, forming channels to guide the exudate down into a clay collecting cup.
Continue reading “Retrotechtacular: The Story Of Turpentine”
A 3D Printed Grinder For Printed Lens Blanks
When one thinks of applications for 3D printing, optical components don’t seem to be a good fit. With the possible exception of Fresnel lenses, FDM printing doesn’t seem up to the job of getting the smooth surfaces and precision dimensions needed to focus light. Resin printing might be a little closer to the mark, but there’s still a long way to go between a printed blank and a finished lens.
That gap is what [Fraens] aims to fill with this homebrew lens grinding machine. It uses the same basic methods used to grind and polish lenses for centuries, only with printed components and lens blanks. The machine itself consists of a motorized chuck for holding the lens blank, plus an articulated arm to hold the polishing tool. The tool arm has an eccentric drive that wobbles the polishing tool back and forth across the blank while it rotates in the chuck. Lens grinding requires a lot of water and abrasive, so a large bowl is provided to catch the swarf and keep the work area clean.
Lens blanks are printed to approximately their finished dimensions using clear resin in an SLA printer. [Fraens] spent a lot of time optimizing the printing geometry to minimize the number of print layers required. He found that a 30° angle between the lens and the resin pool worked best, resulting in the clearest blanks. To polish the rough blanks, a lapping tool is made from polymer modeling clay; after baking it dry, the tool can hold a variety of pads and polishing compounds. From there it’s just a matter of running the blank through a range of abrasives to get the desired final surface.
Are the lenses fantastic? Well, they’re probably not going to make it into fine optical equipment, but they’re a lot better than you might expect. Of course, there’s plenty of room for improvement; better resins might result in clearer blanks, and perhaps degassing the uncured resin under vacuum might help with bubbles. Skipping the printed blanks and going with CNC-machined acrylic might be worth a try, too.
Continue reading “A 3D Printed Grinder For Printed Lens Blanks”
Simple Hack Lets Smartphone Take Resin Printer Time-Lapses
With how cheap they’re getting, everyone seems to be jumping on the resin printer bandwagon. They may not be able to fully replace your trusty old FDM printer, but for certain jobs, they just can’t be beaten. Sadly though, creating those smooth time-lapse videos of your prints isn’t quite as easy to do as it is on their filament-based counterparts.
Not as easy, perhaps, but not impossible. [Fraens] found a way to make time-lapses on any resin printer, and in a wonderfully hacky way. First, you need to find a smartphone, which shouldn’t be too hard, given how often we all tend to upgrade. [Fraens] recommends replacing the standard camera app on the phone with Open Camera, to prevent it from closing during the long intervals with nothing happening. The camera is triggered by any readily available Bluetooth dongle, which is connected via a simple transistor circuit to an Arduino output. To trigger the shutter, a light-dependent resistor (LDR) is connected to one of the microcontroller’s inputs. The LDR is placed inside the bed of the resin printer — an Anycubic Photon in this case — where light from the UV panel used to cross-link the resin can fall on it. A simple bit of Arduino code triggers the Bluetooth dongle at the right moment, capturing a series of stills which are later stitched together using DaVinci Resolve.
The short video below shows the results, which look pretty good to us. There are other ways to do this, of course, but we find the simplicity of this method pleasing.
Continue reading “Simple Hack Lets Smartphone Take Resin Printer Time-Lapses”
Powder Your Prints For Baby-Smoothness
Layer lines are a dead giveaway to non-normies that a thing was 3D printed. There are things you can do to smooth them — sanding, chemical smoothing, and fillers come to mind. Although this technique technically uses all three, it starts with something very simple.
In the video after the break, [DaveRig] gets right to the point: baby powder and resin mixed together make a fine smoothing agent when cured. Having read about it online, he decided to give it a try.
Starting with a half sphere that had admittedly pretty big layer lines, [DaveRig] mixed up enough resin and baby powder to make the consistency of milk or cream. Then he put five coats on, curing and sanding with 120 in between each one.
Then it’s on to standard post-processing stuff. You know, wipe it down with alcohol, sand it a little more, wet sand, and then it’s on to the airbrush and clear-coat. The end result looks to be as smooth as your average bowling ball, as you can see in the main photo.
What’s your favorite post-processing method? Have you tried annealing them in salt?