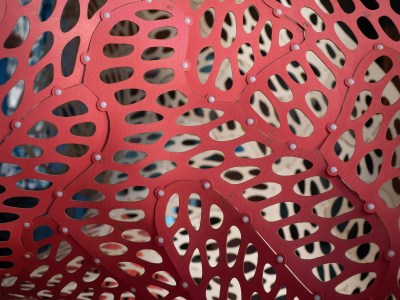
The sculpture shown here is called Puzzle Cell Complex and was created by [Nervous System] as an art piece intended to be collaboratively constructed by conference attendees. The sculpture consists of sixty-nine unique flat panel pieces, each made from wood, which are then connected together without the need for tools by using plastic rivets. Everything fits into a suitcase and assembly documentation is a single page of simple instructions. The result is the wonderfully-curved gyroid pattern you see here.
The sculpture has numerous layers of design, not the least of which was determining how to make such an organically-curved shape using only flat panels. The five-foot assembled sculpture has a compelling shape, which results from the sixty-nine individual panels and how they fit together. These individual panel shapes have each been designed using a technique called variational surface cutting to minimize distortion, resulting in their meandering, puzzle-piece-like outlines. Each panel also has its own unique pattern of cutouts within itself, which makes the panels lighter and easier to bend without sacrificing strength. The short video embedded below shows the finished sculpture in all its glory.
Continue reading “Making A Gorgeously-Twisty Sculpture, Using Only Flat Pieces”