These days, high-quality displays and powerful microcontrollers are cheap and plentiful. That wasn’t the case a couple of decades ago, and so engineers sometimes had to get creative. The result of this is products like the Jaguar nu.yell sewing machine, as covered by [Kelsey Lewin].
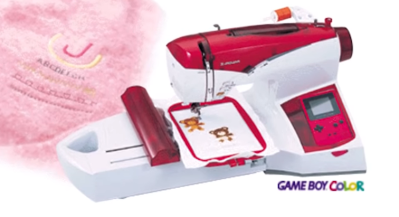
The Japanese market product eschewed the typical mechanical controls of the era, to instead interface with a Nintendo Game Boy. The sewing machine would hook up to the handheld console via the Link Port, while the user ran a special cartridge containing the control software. This would allow the user to select different stitch types, or embroider letters. Very much a product of its time, the nu yell mimics the then-cutting edge industrial design of the first-generation Apple iMac. The technology was later licensed to Singer, who brought it to the US under the name IZEK. Sales were poor, and the later Jaguar nuotto didn’t get a similar rebranding stateside.
Back in the late 90s, the Game Boy was likely an attractive package to engineers. Packing a Z80 processor, buttons, and a screen, it could act as a simple human interface in lieu of designing one from the ground up. Aprilia even used them to diagnose motorbike ECUs, and we’ve seen Game Boy parts used in medical hardware from the era, too. Video after the break.
Continue reading “There Really Was A Sewing Machine Controlled By A Game Boy”