Overseas factories can be sort of a mythical topic. News articles remind us that Flex (née Flextronics) employs nearly 200 thousand employees worldwide or that Foxconn is up to nearly a million. It must take an Apple-level of insider knowledge and capital to organize such a behemoth workforce, certainly something well past the level of cottage hardware manufacturing. And the manufacturing floor itself must be a temple to bead blasted aluminum and 20 axis robotic arms gleefully tossing products together. Right?
Well… the reality is a little different. The special sauce turns out to be people who are well trained for the task at hand and it doesn’t require a $1,000,000,000,000 market cap to get there.
[Adam leeb] was recently overseas to help out with the production ramp for one of his products and took a set of fantastic videos that walk us through an archetypical asian factory.
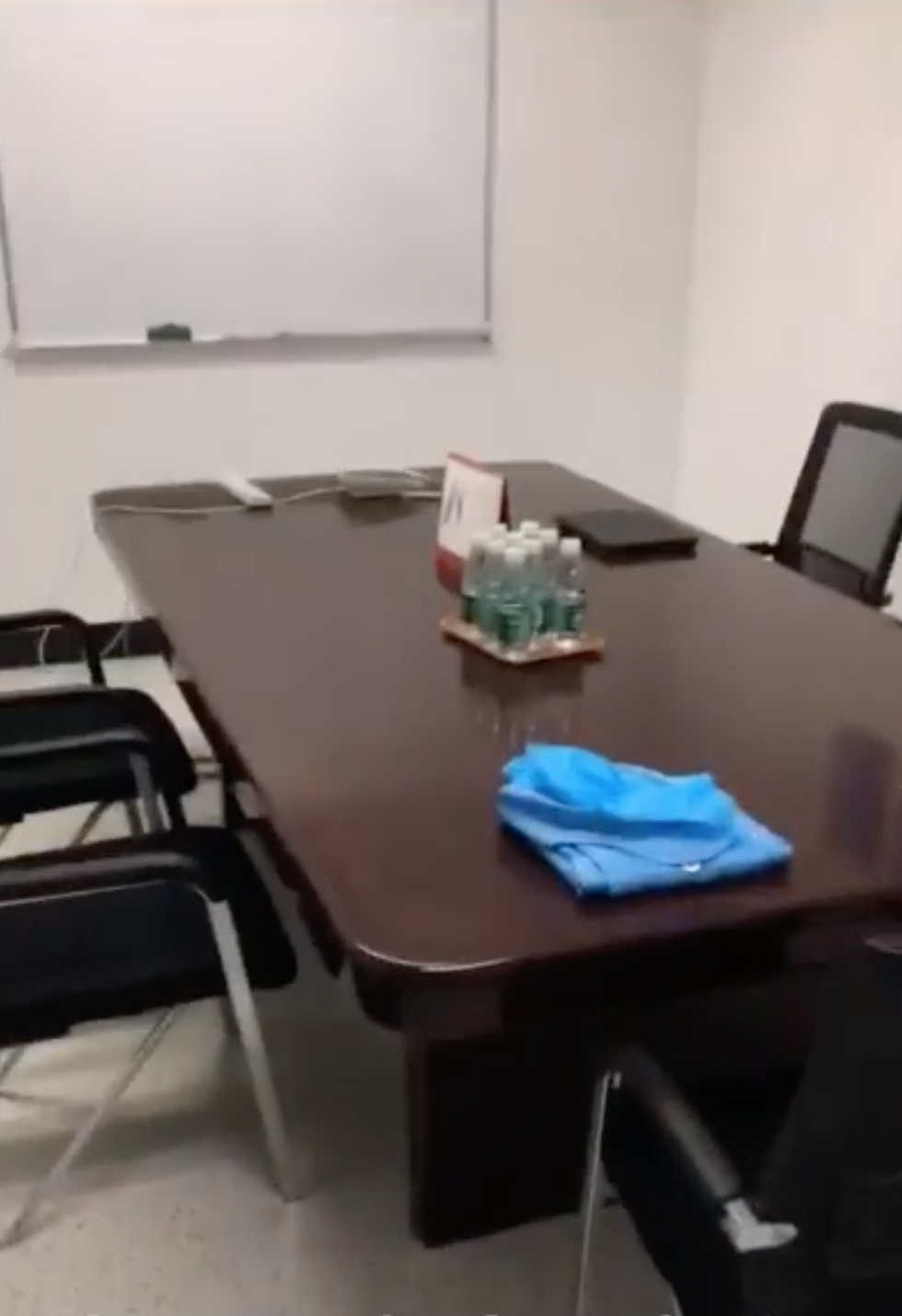
I’ve been to several factories and for me the weirdest part of the archetype is the soul crushing windowless conference room which is where every tour begins. Check out this one on the left. If you ever find yourself in a factory you will also find a room like this. It will have weird snacks and bottles of water and a shiny wood-esque table. It will be your home for many, many more hours than you ever dreamed. It’s actually possible there’s just one conference room in the universe and in the slice of spacetime where you visit it happens to be in your factory.
Ok, less metaphysics. It’s amazing to watch the myriad steps and people involved in taking one product from zero to retail-ready. [adam] gives us a well narrated overview of the steps to go from a single bare board to the fully assembled product. From The Conference Room he travels to The Floor and walks us through rows of operators performing their various tasks. If you’ve been reading for a while you will recognize the pick and place machines, the ovens, and the pogo pin test fixtures. But it’s a treat to go beyond that to see the physical product that houses the boards come together as well.
Check out [adam]’s videos after the break. The first deals with the assembly and test of his product, and the second covers the assembly of the circuit boards inside which is broadly referred to as SMT. Watching the second video you may notice the funny (and typical) contrast between the extremely automated SMT process and everything else.
Continue reading “A Tour Through The Archetypical Asian Factory”