When you think of renewable energy, what comes to mind? We’d venture to guess that wind and solar are probably near the top of the list. And yes, wind and solar are great as long as the winds are favorable and the sun is shining. But what about all those short and bleak winter days? Rainy days? Night time?
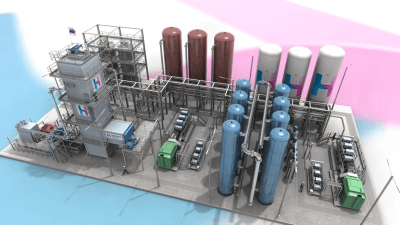
Unfavorable conditions mean that storage is an important part of any viable solution that uses renewable energy. Either the energy itself has to be stored, or else the means to produce the energy on demand must be stored.
One possible answer has been right under our noses all along — air. Regular old ambient air can be cooled and compressed into a liquid, stored in tanks, and then reheated to its gaseous state to do work.
This technology is called Cryogenic Energy Storage (CES) or Liquid Air Energy storage (LAES). It’s a fairly new energy scheme that was first developed a decade ago by UK inventor Peter Dearman as a car engine. More recently, the technology has been re-imagined as power grid storage.
UK utility Highview Power have adopted the technology and are putting it to the test all over the world. They have just begun construction on the world’s largest liquid air battery plant, which will use off-peak energy to charge an ambient air liquifier, and then store the liquid air, re-gasifying it as needed to generate power via a turbine. The turbine will only be used to generate electricity during peak usage. By itself, the LAES process is not terribly efficient, but the system offsets this by capturing waste heat and cold from the process and reusing it. The biggest upside is that the only exhaust is plain, breathable air.
Continue reading “Liquid Air Energy Storage: A Power Grid Battery Using Regular Old Ambient Air”